Download Dynojet Research Port Devices Driver
- Connect to the diagnostic port to fl ash a tune; use the USB connection to interface between the Power Vision and your computer. Download the Power Core software and take tuning to a whole new level. 1 Go to www.dynojet.com/PowerVision. 2 From the top navigation menu, select SupportDownloads.
- This device is also simple to install, and while you're riding, it reads the data coming from the crank and throttle position sensors and automatically adjusts gasoline supply. Everything goes on incredibly fast – when you accelerate under different loads, the Fi2000 makes sure your bike achieves maximum performance possible.
Hi there my name is Mohammad I’m from kuwait and and the owner of 965 company we have some problem when we ordered the Dino jet from Kawasaki company from here in Kuwait they send the dynojets without a plate and there is many problem and the support the board is not working and when I talk with Kawasaki company they don’t care.
©2008 Dynojet Research, Inc. All Rights Reserved.
Model 200iX/250iX Upgrade Installation Guide
This manual is copyrighted by Dynojet Research, Inc., hereafter referred to as Dynojet, and all rights are reserved. This manual, as well as the software described in it, is furnished under license and may only be used or copied in accordance with the terms of such license. This manual is furnished for informational use only, is subject to change without notice, and should not be construed as a commitment by Dynojet. Dynojet assumes no responsibility or liability for any error or inaccuracies that may appear in this manual. Except as permitted by such license, no part of this manual may be reproduced, stored in a retrieval system, or transmitted, in any form or by any means, electronic, mechanical, recording, or otherwise, without the prior written permission of Dynojet.
The Dynojet logo is a trademark of Dynojet Research, Inc.
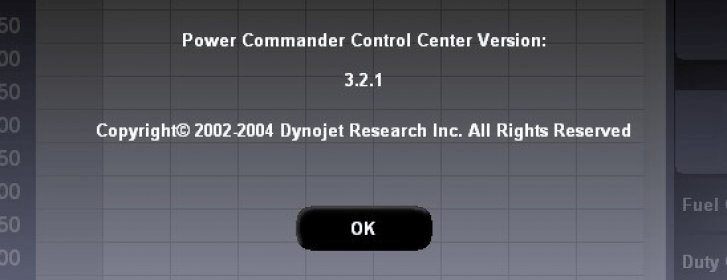
Any trademarks, trade names, service marks, or service names owned or registered by any other company and used in this guide are the property of their respective companies.
Dynojet Research, Inc., 2191 Mendenhall Drive, North Las Vegas, Nevada 89081, USA.
Printed in USA.
Part Number: 98200013 Version 01 (03/2008)
TABLE OF CONTENTS
Warnings . . . . . . . . . . . . . . . . . . . . . . . . . . . . . . . . . . . . . . . . . . . . . . . . iii
Chapter 1 Model 200iX/250iX Upgrade
Introduction . . . . . . . . . . . . . . . . . . . . . . . . . . . . . . . . . . . . . . . . . . . . . . . . . . 1-2
Conventions Used In This Manual . . . . . . . . . . . . . . . . . . . . . . . . . . . . . . . 1-2
Technical Support . . . . . . . . . . . . . . . . . . . . . . . . . . . . . . . . . . . . . . . . . . . 1-2
Model 200iX/250iX Upgrade Specifications . . . . . . . . . . . . . . . . . . . . . . . . 1-3
Chassis Specifications . . . . . . . . . . . . . . . . . . . . . . . . . . . . . . . . . . . . . . . . . 1-3
Dyno Preparation . . . . . . . . . . . . . . . . . . . . . . . . . . . . . . . . . . . . . . . . . . . . . 1-6
Disconnecting the Power . . . . . . . . . . . . . . . . . . . . . . . . . . . . . . . . . . . . . .1-6
Removing the High Pressure Blower Assemblies . . . . . . . . . . . . . . . . . . . . . 1-7
Removing the Monitor Stand . . . . . . . . . . . . . . . . . . . . . . . . . . . . . . . . . . . 1-8
Removing the Dyno Panels . . . . . . . . . . . . . . . . . . . . . . . . . . . . . . . . . . . .1-9
Drum Installation . . . . . . . . . . . . . . . . . . . . . . . . . . . . . . . . . . . . . . . . . . . . . 1-10
Removing the Items from Crate . . . . . . . . . . . . . . . . . . . . . . . . . . . . . . . . 1-10
Installing the iX Drum Module . . . . . . . . . . . . . . . . . . . . . . . . . . . . . . . . . 1-12
Bulkheads and Covers . . . . . . . . . . . . . . . . . . . . . . . . . . . . . . . . . . . . . . . . . 1-15
Installing the Bulkheads . . . . . . . . . . . . . . . . . . . . . . . . . . . . . . . . . . . . . . 1-15
Installing the Panels and Covers . . . . . . . . . . . . . . . . . . . . . . . . . . . . . . . . 1-17
Trike Carriage Adapter Installation . . . . . . . . . . . . . . . . . . . . . . . . . . . . . .1-20
Removing the Carriage Screw and Carriage . . . . . . . . . . . . . . . . . . . . . . .1-21
Removing the Carriage Clamps, Shims, and Nut Block . . . . . . . . . . . . . . . 1-22
Installing the Trike Carriage Adapter Assembly . . . . . . . . . . . . . . . . . . . . . 1-23
Installing the Carriage Assembly . . . . . . . . . . . . . . . . . . . . . . . . . . . . . . . .1-24
Tie-Down Installation . . . . . . . . . . . . . . . . . . . . . . . . . . . . . . . . . . . . . . . . . 1-25
Monitor Stand and Blowers Installation . . . . . . . . . . . . . . . . . . . . . . . . . .1-26
Ground Hook Installation . . . . . . . . . . . . . . . . . . . . . . . . . . . . . . . . . . . . . .1-28
i
Chapter 2 Basic Dyno Operation
Loading the Vehicle . . . . . . . . . . . . . . . . . . . . . . . . . . . . . . . . . . . . . . . . . . . 2-2
Connecting the RPM Pickup . . . . . . . . . . . . . . . . . . . . . . . . . . . . . . . . . . . . 2-4
RPM Pickup Descriptions . . . . . . . . . . . . . . . . . . . . . . . . . . . . . . . . . . . . . .2-4
Connecting the Secondary Inductive Pickup . . . . . . . . . . . . . . . . . . . . . . . 2-5
Connecting The Primary Inductive Pickup . . . . . . . . . . . . . . . . . . . . . . . . .2-6
Pre-Run Inspection . . . . . . . . . . . . . . . . . . . . . . . . . . . . . . . . . . . . . . . . . . . . 2-7

Before Starting the Engine . . . . . . . . . . . . . . . . . . . . . . . . . . . . . . . . . . . . . 2-8
Engine Warm Up . . . . . . . . . . . . . . . . . . . . . . . . . . . . . . . . . . . . . . . . . . . .2-8
After Engine Warm Up . . . . . . . . . . . . . . . . . . . . . . . . . . . . . . . . . . . . . . . . 2-8
Making a Test Run . . . . . . . . . . . . . . . . . . . . . . . . . . . . . . . . . . . . . . . . . . . . 2-9
Preventative Maintenance . . . . . . . . . . . . . . . . . . . . . . . . . . . . . . . . . . . . . 2-10
Appendix A Red Head Anchor Installation
Installation . . . . . . . . . . . . . . . . . . . . . . . . . . . . . . . . . . . . . . . . . . . . . . . . . . .A-2
Appendix B Ramp Kit Installation
Ramp Installation . . . . . . . . . . . . . . . . . . . . . . . . . . . . . . . . . . . . . . . . . . . . . . B-2
Index . . . . . . . . . . . . . . . . . . . . . . . . . . . . . . . . . . . . . . . . . . . . . . . . . Index-i
ii
WARNINGS
Disclaimers
Dynojet Research, Inc. (Dynojet) makes no representation or warranties with respect to the contents hereof and specifically disclaims any implied warranties of merchantability for any particular purpose.
Dynojet reserves the right to revise this publication and to make changes from time to time in the content hereof without obligation of Dynojet to notify any person of such revision or changes.
Dynojet is not responsible for false operation due to unexpected dynamometer operation such as may be caused by static, software bugs, hardware failure, etc.
Dynojet is not responsible for damage resulting from improper installation of the dynamometer or from improper service rendered to the dynamometer. Dynojet is not responsible for damage incurred due to alteration of the dynamometer or components, use of unapproved parts, or abuse to the dynamometer.
Do not connect or disconnect cables or components on the dynamometer with the power on.
Always wear protective clothing, ear protection, and eye protection (goggles, safety glasses) when using and servicing the dynamometer.
Equipment Power Requirements
The dynamometer has specific power requirements. Connecting the dynamometer to the incorrect voltage will void the dynamometer warranty. Installation may require a licensed electrician.
Potentially Lethal Voltages
Components attached to and within the dynamometer operate with potentially lethal voltages. To provide the greatest assurance of safety, the AC power cord(s) must be disconnected from the power source before servicing electrical components or wiring. Disconnect all power cords before servicing electrical components for the greatest assurance of safety.
iii
Electrostatic Discharge Precautions
Electrostatic Discharge
Electrostatic Discharge (ESD), or static shock, can damage electronic components within the dynamometer. The damage may occur at the time of an ESD occurrence, or the shock may degrade the component, resulting in a premature component failure later. To avoid ESD damage, always practice good ESD control precautions when servicing the dynamometer. Dynojet designs its dynamometers to be very tolerant of static shocks by the users, but the electronics are vulnerable when the electronics are exposed. ESD occurs as a result of a difference of potential between two objects when the two objects touch. Damage occurs as a result of the energy released when the discharge (touch) occurs. The difference of potential can accumulate by as simple an action as a user moving across carpet or a seat. If that person’s energy is discharged directly to the electronics, the electronics can be damaged.
Bit Driver Updater helps computers to detect defective drivers, install driver updates when needed, and fix other driver-related issues. Supercharged Performance Keeps your system drivers up-to-date for better hardware compatibility and to deliver top-notch Windows performance. InnoTek Systemberatung GmbH VirtualBox Graphics Adapter Hardware ID PCIVEN80EE&DEVBEEF Select the driver for your operating system and its bit. It is recommended to install a later version of the driver (see the release date). To go to the download file, click on the link. Driver ICs/Motor Drivers: Datasheet: TRINAMIC Motion Control GmbH TMC5130A-TA-T. RoHS: Package: TQFP-48: Manufacturer: TRINAMIC Motion Control GmbH: Brand Category: International Brands: Packaging: Tray 0 products found. Pinnacle systems gmbh driver. Drivers Library We know a lot about PC drivers. Welcome to the PC Matic Driver Library, the internet's most complete and comprehensive source for driver information. Innotek gmbh Driver Downloads. To find the latest driver for your computer we recommend running our Free Driver Scan. Your GMB membership provides you with lots of additional benefits and offers, over and above GMB's assistance in your workplace, providing a whole range of products that.
Precautions
To protect against ESD damage, you must eliminate the difference of potential before the electronics are handled. Touch the chassis of the dynamometer before touching any of the electronics. By touching the chassis, you discharge any static shocks to the chassis instead of to the electronics.
If you are holding a circuit board or dynamometer component in your hand when you approach the machine, touch the chassis of the dynamometer with your hand before installing the circuit board or component.
When handling a circuit board or component to someone, touch that person with your hand first, then hand them the component.
Always carry circuit boards in anti-static bags when the boards are exposed (removed from the dynamometer). Dibcom input devices driver download for windows.
Battery Fire and Explosion Hazards
There is a danger of explosion if the battery is incorrectly replaced. Replace only with the same or equivalent type recommended by the manufacturer. Discard used batteries according to the manufacturer’s instructions.
Automotive Batteries
In operation, batteries generate and release flammable hydrogen gas. They must always be assumed to contain this gas which, if ignited by burning cigarette, naked flame or spark, may cause battery explosion with dispersion of casing fragments and corrosive liquid electrolyte. Carefully follow manufacturer's instructions for installation and service. Keep away all sources of gas ignition and do not allow metallic articles to simultaneously contact the negative and positive terminals of a battery.
Do not allow the positive and negative terminals to short-circuit. The dynamometer chassis is tied to the negative side of the battery. Do not short between the positive battery terminal or the starter connections to the chassis. In addition, make sure metal tools such as screw drivers, wrenches, and torque wrenches do not come in contact with the negative and positive terminals of the battery. Short circuiting the terminals of the battery can cause burn injuries, damage to the dynamometer, or trigger explosions.
Charging
Batteries being charged will generate and release flammable hydrogen gas. Charging space should be ventilated. Keep battery vent caps in position. Prohibit smoking and avoid creation of flames and sparks nearby.
Wear protective clothing, eye and face protection, when charging or handling batteries.
iv
WA R N I N G S
Other Potential Hazards
The AC power outlet shall be installed near the equipment and it shall be easily accessible to allow for disconnect before service.
The dynamometer should be located in a well ventilated area. There is a carbon monoxide hazard with all internal combustion engines. Engine exhaust contains poisonous carbon monoxide gas. Breathing it could cause death.
Any dyno room design must incorporate sufficient exhaust extraction.
Always wear proper ear and eye protection when operating the dynamometer. Never operate the dynamometer with the covers removed.
Never stand behind the dynamometer when in operation.
Never operate the dynamometer when there is excessive vibration or noise. Resolve these problems before proceeding.
Never fuel the vehicle on the dynamometer unless appropriate safety measures are taken. Verify brake operation before beginning any dynamometer testing.
Verify the vehicle is properly secured to the dynamometer. Never operate the blowers without the guards installed.
Exercise care with any dynamometer testing; portions of the dynamometer and vehicle may become hot.
As with any equipment using electricity and having moving parts, there are potential hazards. To use this dynamometer safely, the operator should become familiar with the instructions for operation of the dynamometer and always exercise care when using it.
Do not repair or replace any part of the dynamometer or attempt any servicing unless specifically recommended in published user-repair instructions that you understand and have the skills to carry out.
v
Version 1 | Model 200iX/250iX Upgrade Installation Guide |
C H A P T E R
1
MODEL 200IX/250IX UPGRADE
Thank you for purchasing the 200iX/250iX upgrade for Dynojet’s Model 200i/250i Motorcycle Dynamometer. This upgrade will allow you to run a kart, ATV, or trike on your motorcycle dynamometer. Dynojet’s software and dynamometers will give you the power to get the maximum performance out of vehicles you evaluate. Whether you are new to the benefits of a chassis dynamometer or an experienced performance leader, the repeatability and diagnostic tools of WinPEP 7 software and a Dynojet dynamometer will give you the professional results you are looking for.
This document provides instructions for installing the 200iX/250iX upgrade to Dynojet’s Model 200i/250i Motorcycle Dynamometer (dyno). This document will walk you through the installation and basic dyno operation along with installing the optional ramp. To ensure safety and accuracy in the procedures, perform the procedures as they are described.
Document Part Number: 98200013 Version 1
Last Updated: 03-07-08
This section is divided into the following categories:
•Introduction, page 1-2
•Model 200iX/250iX Upgrade Specifications, page 1-3
•Dyno Preparation, page 1-6
•Drum Installation, page 1-10
•Bulkheads and Covers, page 1-15
•Trike Carriage Adapter Installation, page 1-20
•Tie-Down Installation, page 1-25
•Monitor Stand and Blower Installation, page 1-26
•Ground Hook Installation, page 1-28
1-1
C H A P T E R 1
Introduction
INTRODUCTION
. . . . . . . . . . . . . . . . . . . . . . . . . . . . . . . . . . .
Before installing your 200iX/250iX upgrade, please take a moment to read this guide for installation instructions, dyno features, and other important information.
CONVENTIONS USED IN THIS MANUAL
The conventions used in this manual are designed to protect both the user and the equipment.
example of convention | description | ||||
The Caution icon indicates a potential hazard to the | |||||
dynamometer equipment. Follow all procedures | |||||
exactly as they are described and use care when | |||||
performing all procedures. | |||||
The Warning icon indicates potential harm to the | |||||
person performing a procedure and/or the | |||||
dynamometer equipment. |
TECHNICAL SUPPORT
For assistance, please contact Dynojet Technical Support at 1-800-992-3525, or write to Dynojet at 2191 Mendenhall Drive, North Las Vegas, NV 89081.
Visit us on the World Wide Web at www.dynojet.com where Dynojet provides state of the art technical support, on-line shopping, and press releases about our latest product lines.
1-2
M O D E L 2 0 0 I X / 2 5 0 I X U P G R A D E
Model 200iX/250iX Upgrade Specifications
MODEL 200IX/250IX UPGRADE SPECIFICATIONS
. . . . . . . . . . . . . . . . . . . . . . . . . . . . . . . . . . .
The following specifications and requirements will help you set up your dyno area for the 200iX/250iX upgrade.
Download Dynojet Research Port Devices Driver
Refer to the model 200i/250i installation guide for specifications and requirements for the bike dyno.
CHASSIS SPECIFICATIONS
description | specifications |
Length | |
dyno with standard carriage | allow 271.78 cm (107.00 in.) |
dyno with extended carriage | allow 322.58 cm (127.00 in.) |
dyno with ramp | 370.84 cm (146.00 in.) |
Height | |
to top of dyno cover | 45.97 cm (18.00 in.) |
Width | |
model 200i/200iX upgrade | 200.69 cm (79.00 in.) |
model 250i/250iX upgrade | 274.32 cm (108.00 in.) |
Weight | |
200iX/250iX drum module/crated | 136 kg (300 pounds)/272 kg (600 pounds) |
Drum | |
diameter, 200iX/250iX upgrade | 45.72 cm (18.00 inches) |
width, 200iX/250iX upgrade | 55.88 cm (22.00 inches) |
Frame | structural steel channel and angle |
Maximum Speed | 322 KPH (200 MPH) |
Maximum Motorcycle Length (front of | |
front wheel to center of rear wheel) | |
standard carriage | 213 cm (84.00 inches) |
extended carriage | 256.54 cm (101.00 inches) |
Remote Switches | remote software control |
1-3
Version 1 | Model 200iX/250iX Upgrade Installation Guide |
C H A P T E R 1
Model 200iX/250iX Upgrade Specifications
Figure 1-1: Model 250iX Dyno Dimensions
1-4
M O D E L 2 0 0 I X / 2 5 0 I X U P G R A D E
Model 200iX/250iX Upgrade Specifications
Folding Ramp Option | Eddy Current | Monitor Support |
(Dyno) | Brake | and Tray |
High Pressure
Blower
Wheel Clamp | |
Option | |
Folding Ramp Option | |
(iX Upgrade) | Power Carriage |
Option | |
Model 250i Dyno | |
iX Drum Module | |
Trike Carriage | |
Adapter | |
iX Upgrade | |
Figure 1-2: Model 250iX Dyno with Accessories |
1-5
Version 1 | Model 200iX/250iX Upgrade Installation Guide |
C H A P T E R 1
Dyno Preparation
DYNO PREPARATION
. . . . . . . . . . . . . . . . . . . . . . . . . . . . . . . . . . .
Use the following instructions to prepare the dyno for installing the upgrade kit.
DISCONNECTING THE POWER
Use the following steps to connect and disconnect power to the dyno.
Always turn the power off when connecting and disconnecting cables.
1Use the main breaker to turn power on and off to the dyno.
The main breaker is located inside the CPI door. When the handle is in the down position all power into the dyno is turned off.
2Disconnect the power plug to ensure all power has been removed from the dyno before performing certain installation procedures.
power plug
main breaker
Figure 1-3: Main Dyno Power
1-6
M O D E L 2 0 0 I X / 2 5 0 I X U P G R A D E
Dyno Preparation
REMOVING THE HIGH PRESSURE BLOWER ASSEMBLIES
1Unplug each high pressure blower power cord from the dyno chassis.
2Remove the clamp lever securing the blower arm assembly to the dyno and discard. Do this for both blower assemblies.
3Lift the blower and arm assembly from the dyno and set aside. Do this for both blower assemblies.
Note: Both blower assemblies must be removed in order to replace the lower blower arm. A new lower blower arm is needed to work with the new upgrade tiedowns.
blower and arm assembly
clamp lever
power cord from blower
Figure 1-4: Removing the Blower Assemblies
1-7
Version 1 | Model 200iX/250iX Upgrade Installation Guide |
C H A P T E R 1
Dyno Preparation
REMOVING THE MONITOR STAND
1Disconnect all cables from the monitor stand.
2Remove the monitor arms and tray.
3Remove the four screws securing the monitor support and set aside.
4Remove the monitor support and set aside.
Download Dynojet Research Port Devices Drivers
monitor tray
monitor arms
monitor support
Figure 1-5: Removing the Monitor Stand
1-8
M O D E L 2 0 0 I X / 2 5 0 I X U P G R A D E
Dyno Preparation
REMOVING THE DYNO PANELS
1Push the wires, from the monitor stand, back through the cable pass through.
Note: Perform this step only if the monitor stand was installed on the right side of the dyno.
2Remove the five screws securing the top panel to the dyno and set aside. Remove the top panel and set aside.
3Disconnect the fan power cable from the power socket on the inside of the side panel.
4Remove the eight screws securing the drum side panel to the dyno and set aside. Remove the panel and set aside.
5Remove the twelve screws securing the side panel to the dyno and set aside. Remove the side panel and set aside.
drum side panel
top panel
side panel | cable pass | fan power |
through | socket |
Figure 1-6: Removing the Dyno Panels
1-9
Version 1 | Model 200iX/250iX Upgrade Installation Guide |
FAQs
All Widebandcommander FAQs
Can the Wide Band Commander plug directly into my Power Commander for automatic tuning or channel retrieval? Back to Top
The Wide Band Commander is a stand alone product that is not designed to communicate with the Power Commander or plug directly to the Power Commander's expansion port. The information retrieved from the Wide Band Commander can be used to adjust the Power Commander's map.
I have a Wide Band Commander and a Power Commander installed on my motorcycle, how can I adjust the map? Back to Top
The Power Commander's map is based off positive and negative whole numbers versus RPM and Throttle Position. Positive numbers add fuel and negative numbers remove fuel. If the air-fuel ratio (for Unleaded Petrol) is closer to 18:1, the vehicle is lean and when it is near 10:1 the vehicle is rich. When the numbers are adjusted based off of the Wide Band Commander's information, it will allow the air-fuel reading to be set to a more optimal ratio. The maps that are designed by Dynojet , directly, are tuned to have a ratio ranging from 13:1-13.8:1.
For the best tune against air-fuel ratio, horsepower, and torque, it is recommended that a custom map be made at a Power Commander Tuning Center. These facilities are set-up all over the world and have the capability of adjusting the bike for all around optimal performance using a Dynojet Load Control Dynamometer with air-fuel ratio monitor. Please visit the following link to locate a local Power Commander Tuning Center within your area: www.powercommander.com.
Why do I need a wide band A/F sensor? I can buy a kit that ties into my factory oxygen sensor for a lot less money. Back to Top
A typical production vehicle uses oxygen sensors that have a very narrow resolution. When you are cruising / idling (closed loop), the vehicle is concerned with maintaining an A/F ratio of 14.7 (stoich). When you put your foot on the floor and go into power enrichment (open loop), the factory sensors do not have enough resolution to tell you an exact A/F ratio. Any system that ties in to the factory oxygen sensors can only tell you if you are richer or leaner than 14.7. The Wide Band Commander, utilizing the Bosch LSU4 wideband sensor, will tell you exactly what A/F ratio you are running.
What A/F ratio should I be looking for when I'm tuning? Back to Top
On a naturally aspirated engine, you'll make best / safe power between 12.8-13.2. Vehicles running 'power adders' will need to run a little richer, between 11.5-12.5 for best / safe power.
I bought a wide band kit from someone other than Dynojet, but I like your gauge better, is it available for sale? Back to Top
The gauge is available separately, but it may not work with competitors systems.
My vehicle utilizes a coil-on-plug ignition system, do I need a tach adapter to allow the WBC to 'see' RPM? Back to Top
The WBC uses the same RPM acquisition technology found on our world class dynamometers. It is NOT necessary to run an aftermarket tach adaptor, the WBC includes the harness (1 wire hook up) to acquire an RPM signal.
What is the 'Programmable Relay Output'? Back to Top
This output is designed to control the ground circuit on a relay system. The software is configurable to control the circuit based on 1, 2, or all 3 of the WBC inputs. Here's an example, lets say you have a nitrous oxide system on your vehicle. You would tie the 'Programmable Relay Output' wire into the wire that provides the ground for the relay on the nitrous system. The WBC software allows you to define the logic as follows - 'if TP is greater than 3v, and if RPM is greater than 3k, and A/F is less than 13.2:1' - then go ahead and provide a ground path for the circuit. If you would like to simplify this logic, you could just say - 'if RPM is greater than 3k' - then go ahead and provide a ground path. There are many different strategies and logic available with this provision!
I don't have a laptop computer, can I still use the WBC? Back to Top
You can certainly still use the WBC effectively without a laptop computer. If you choose to only wire in the WBC module, the sensor, and the gauge, you won't have to configure the TP and RPM channels in the software. When you do choose to install the TP and RPM channels, they do require a configuration routine available through the WBC software.
Do I need a laptop to datalog? Back to Top
NO! You can datalog 1 of 2 ways, either to the laptop using the WBC software, or directly to the WBC module using its internal memory. If you want to log without a laptop, simply install a switch on the appropriate wire on the WBC module (refer to the installation guide). You can download the log session at a later time when it's convenient to you!
Does the WBC system replace my factory oxygen sensors? Back to Top
Absolutely not! The WBC kit includes the appropriate weld boss that needs to be welded in a location that is defined in the installation guide.
Does the sensor also carry a 12 month warranty like the rest of the kit? Back to Top
The sensor itself is not covered under this warranty.
The WBC requires a 'key on' 12v source, where can I find this on my vehicle? Back to Top
The best place to find a 'key on' 12v source is at, or near the fuse block. Be sure to make sure that the source is 'key on', otherwise you'll drain the battery. The WBC sensor REQUIRES power any time the vehicle is running!
Is the WBC waterproof? Back to Top
Even though the WBC is housed in an enclosure, and the circuit board is potted, the unit is considered water resistant. We highly recommend installing the WBC in an area that is free from moisture, heat, and dirt.
I have other gauges in my car and I would like to match their look, do you offer other styles of gauges? Back to Top
Our initial release is only available with black bezel / white face, or silver bezel / black face gauges. In the future we will be releasing other gauges, both digital and analog, to meet the demands of our customers.
I have a stand alone engine management system in my vehicle, does the WBC have an output I can use? Back to Top
Yes, the WBC does have a 0-5v or 0-5 mA linear output.
Why does my WBC seem to log data quicker when I’m using the internal memory as opposed to logging to my laptop? Back to Top
Due to system resources on your laptop, the log sample may not be as quick as the internal logging feature. To optimize the sample rate (up to 10 / sec), we advise that you use the internal logging feature.
How long is the cable from the sensor to the WBC control module? Back to Top
72'
I have an aftermarket ignition system on my vehicle, will I have a problem getting an RPM signal? Back to Top
Even though many aftermarket ignition systems / plug wires emit more noise than the OEM system, the WBC won’t have any issues acquiring a signal. There are provisions in the software to configure the sensitivity to meet you needs.
Can I use a USB adapter to attach to the RS232 serial port on my laptop for configuring and downloading in the car? Back to Top
We have found that this method either does not work at all, or is completely unstable. It is best to use PC / laptop configured with a USB port.
Are software / firmware updates covered with the initial purchase price? Back to Top
All software updates will be free of charge and can be downloaded by visiting our downloads section. Firmware updates can be made in the field, there is no need to send the unit back to Dynojet.
I received a 9v power adapter with my WBC kit, what's it for? Back to Top
The 9v power adapter plugs into the white connector (10 pin) on the side of the WBC. It is used to power up the WBC in the event that you didn't have it wired to a 12v source. We envision most people will leave the WBC hard wired to their vehicle, but a few people may do a 'temporary / mobile install'. This will allow you to power up the WBC in a remote location to download any log sessions or even configure the light / relay with their PC.
Playing back the datalog sessions in the software is a nice feature, but can I export the data to Excel? Back to Top
Yes, when you have a datalog session open, you can go to the “File” menu and select “Export Data”. This will allow you to export the data as a text file, and from there you can save it in a format that can be imported easily into Excel.
I'm interested in the Power Commander and the Wide Band Commander, what's the difference? Back to Top
The Power Commander is a device that allows you to make changes to the fueling characteristics of your vehicle. The Wide Band Commander is a device that allows you to monitor / review how rich or lean your vehicle is running. Currently we only have Power Commander applications for motorcycles (www.powercommander.com), but the Wide Band Commander can be used on most anything with a 12v source and burns petrol fuel!
I noticed my TPS display in the software is not stable, why is this? Back to Top
This can be caused by a poor ground. If both ground wires are grounded to a very good ground, then the digital ground wire (black/wht) should not be affected by the heater ground (black). To get the best possible TPS reading on the Wide Band Commander, connect the blk/wht ground to the TPS ground and the heater ground (blk) to the engine or battery cable.
There isn't a gauge pod available for my vehicle, so I'm thinking about mounting the gauge in different location . What are the dimensions of the gauge? Back to Top
The gauge is a standard 2 1/16' like most of the other performance gauges in the market.
Will the WBC keep my settings in the event I disconnect the battery or lose power? Back to Top
Download Dynojet Research Port Devices Driver Windows 7
The settings you define in the 'Device Settings' will be saved in the event that the WBC loses power. The WBC stores these settings in a non-volatile EEPROM environment.
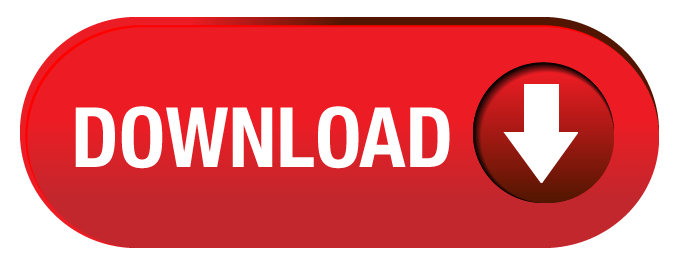